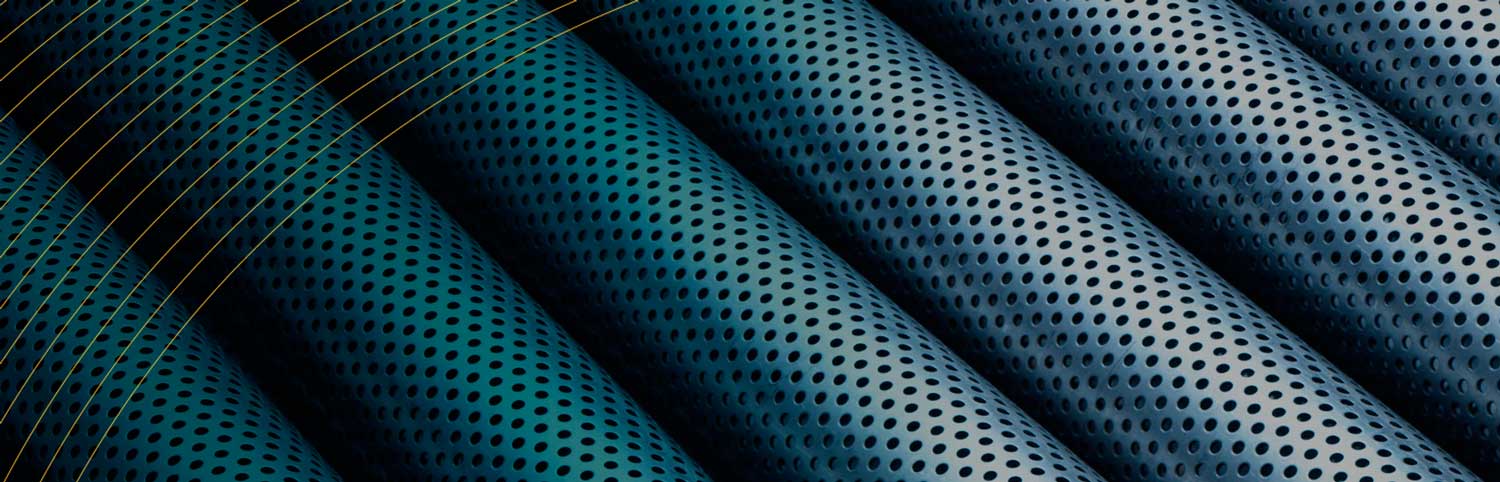
Servicio de consultoría industrial
Trazabilidad 360º: encuentra, en una misma compañía, todos servicios que te interesan: desde el diseño e ingeniería iniciales, hasta la fabricación y atención post-venta.
Cuando todas estas fases durante el desarrollo y montaje de un producto van de la mano bajo el paraguas de NORTEK, aplicando las más altas exigencias en cada una de ellas, solo puedes obtener una solución 100% satisfactoria para ti, ya seas fabricante, ingeniería responsable de proyecto o cliente final.
Conoce nuestros servicios y descubre cómo puedes mejorar la rentabilidad de tu negocio gracias a cada uno de ellos.
Amplia gama de productos para el control de fluidos y lubricación
100%
Ingenieros & Fabricantes
El conocimiento acumulado de más de 50 años a tu alcance
Ingeniería y consultoría
Un despacho de ingenieros especializados a tu disposición
NORTEK es:
- – Asesoramiento,
- – Investigación,
- – Diseño de soluciones a medida
- – Realización de estudios
- – Cálculos previos para cada proyecto
- – Fabricación y montaje
Esto es posible gracias al equipo de ingenieros expertos en nuestras sedes de Pinseque (Zaragoza, España) y Auburn (Massachusetts, Estados Unidos).
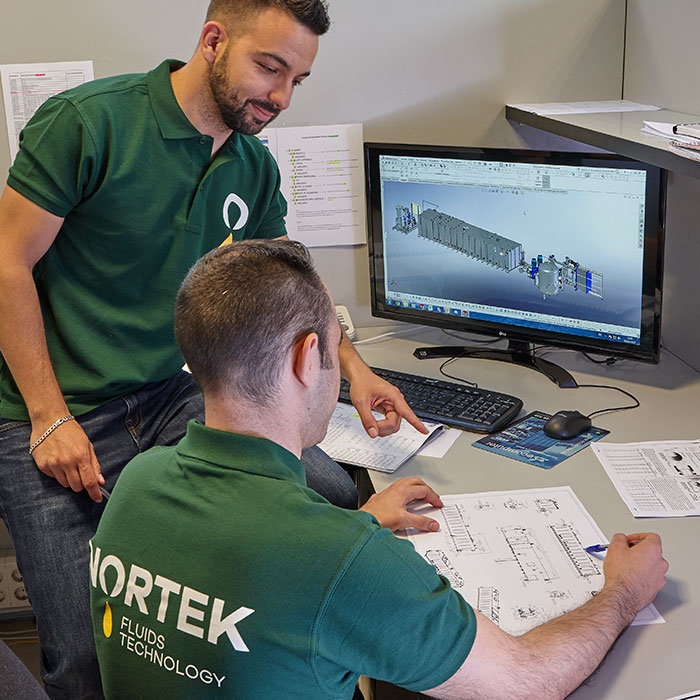
Somos una empresa de ingenieria
Nos gusta considerarnos una empresa de ingeniería que, además, tiene su propia fábrica.
La suma de todo ello resulta en una trazabilidad 360º así como en el desarrollo de soluciones de lubrificación y gestión de fluidos, que diseñamos desde cero específicamente para ti y que cumplen los requisitos normativos más exigentes.
¿Qué obtienes de nuestro servicio de ingeniería y consultoría?
Estas son algunas de nuestras competencias:
- Toma de datos en campo
- Diseño a medida de sistemas de lubrificación y refrigeración
- Cálculos de consumo de aceite en rodamientos y cojinetes
- Cálculos de necesidades de refrigeración en engranajes
- Asesoría sobre lubricantes
- Simulaciones 3D del comportamiento de fluidos en depósitos
- Cálculos de necesidades de filtración
- Diseño de filtros a medida para cualquier fluido
- Dimensionamiento, trazado y optimización de instalaciones de tubería
- Cálculos de caudalímetros
- Diseño de depósitos a presión homologados
- Adaptación de equipos en plantas existentes
- Cálculos de consumo de agua, aire o fluidos hidráulicos
- Suministro de instalaciones de fluidos para nuevas instalaciones
Un servicio con entidad propia y experiencia en el sector industrial
La ingeniería es uno de los pilares fundamentales en NORTEK, que se apoya en el conocimiento acumulado a lo largo de más de cinco décadas y en nuestros continuos procesos de I+D+i. Toda una ventaja que siempre juega en tu beneficio.
Así mismo, nuestra larga experiencia tanto en la renovación de antiguas instalaciones como en el suministro integral de nuevas plantas nos convierte en tu aliado de confianza para revisar instalaciones de lubrificación y fluidos de cara a su auditoría técnica, optimización y renovación.
Fabricación propia de equipo industrial
Fabricación propia, control total en todas las etapas del proceso
La fabricación propia, junto a la labor de nuestro departamento de ingeniería, es una de las grandes señas de identidad que nos definen, permitiéndonos ser flexibles y mostrar una ágil capacidad de respuesta.
Somos una planta de producción polivalente en la que seguimos apostando por la fabricación propia, el conocimiento profundo de productos y procesos, y el control de calidad más exigente.
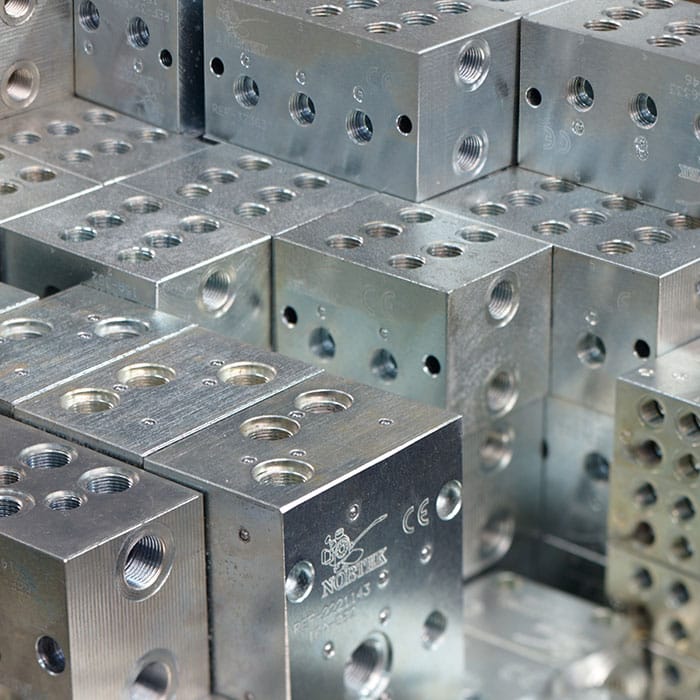
Somos una planta de producción polivalente en la que seguimos apostando por la fabricación propia, el conocimiento profundo de productos y procesos, y el control de calidad más exigente.
¿Qué ventajas te ofrece la fabricación propia?
Tendrás de tu lado un equipo de especialistas capaces de ocuparse íntegramente de:
- Mecanización de componentes para el control, el transporte y la distribución de fluidos
- Producción y ensamble de componentes para la distribución de grasa, aceite y aire-aceite
- Pequeña y gran calderería
- Filtros y elementos filtrantes
- Soldadura certificada según ISO 3834-3
- Chorreado y pintura de componentes hasta 24 m y 12 t
- Ejecución de tubería on-board sobre equipo del cliente Fabricación de bancadas
- Diseño y programación de paneles eléctricos
- Manipulación de componentes de acero inoxidable en nave independiente
- Control de calidad
Del despacho de ingeniería, al taller de fabricación en la misma empresa
Nuestros talleres de calderería, mecanización, precisión y eléctrico, junto con las cabinas de chorreado y pintura, surten la mayor parte de componentes y operaciones necesarios para la producción de nuestros sistemas.
Por eso, gracias a un equipo de profesionales con amplia experiencia en el sector, tenemos la capacidad de materializar lo que diseñamos con un alto nivel de autosuficiencia gracias además al personal especializado presente en todas las fases del proceso productivo.
Investigación y desarrollo para aumentar y mejorar la eficiencia
Investigación y desarrollo: preparados para el siguiente reto
Nuestra implicación en muy diversos sectores y procesos industriales (desde el siderometalúrgico al petroquímico, pasando por minería, papelera, power energy y muchos otros) nos permite mantenernos al tanto de las necesidades específicas de cada aplicación, especialmente en materia de fluidos y transferencia de calor.
Nos planteamos constantemente los nuevos retos que deben afrontar las empresas con las que colaboramos y tenemos presentes los problemas que, tradicionalmente, han presentado difícil solución. Esto nos permite poner a tu alcance soluciones novedosas y eficientes cuando lo necesites.
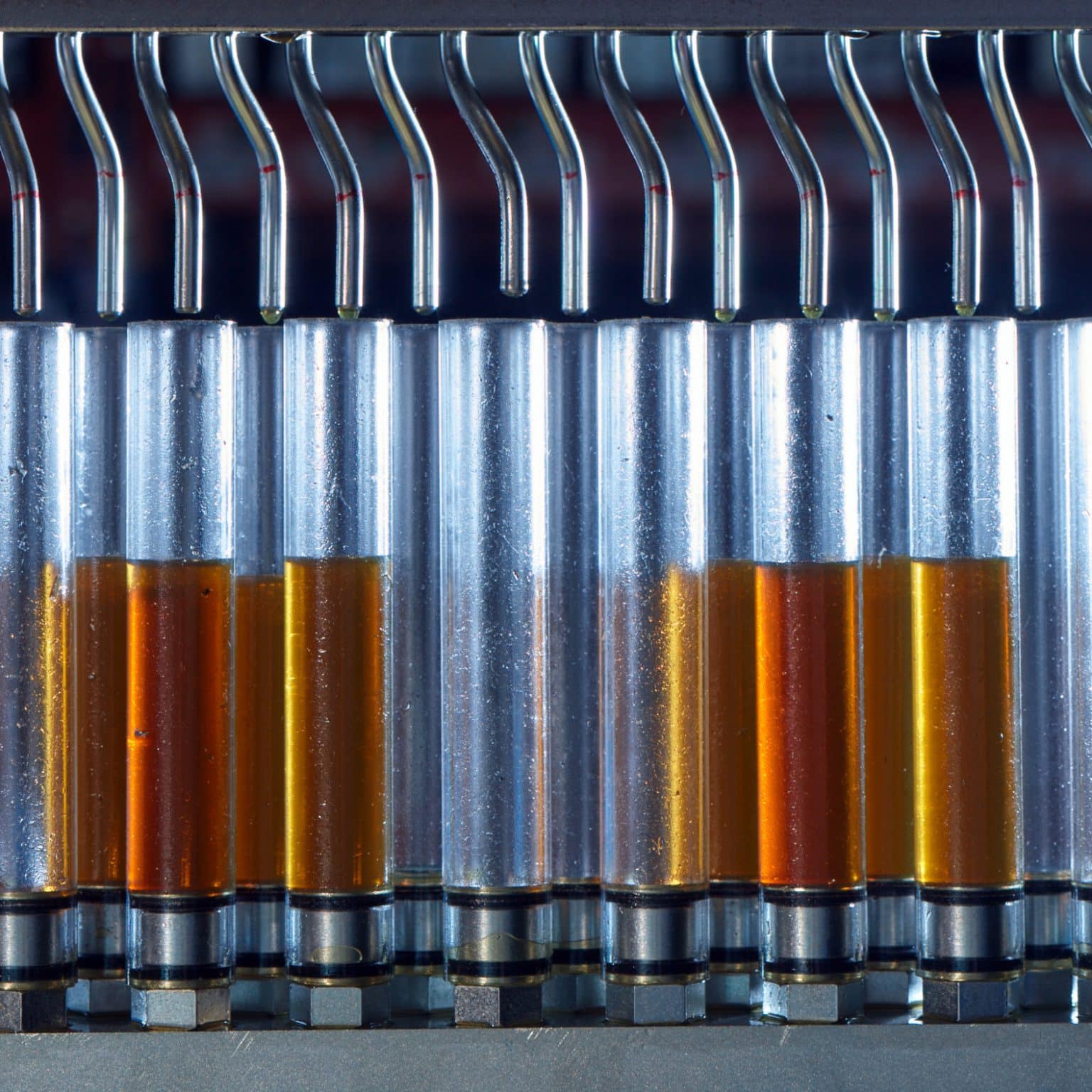
Nos planteamos constantemente los nuevos retos que deben afrontar las empresas con las que colaboramos y tenemos presentes los problemas que, tradicionalmente, han presentado difícil solución. Esto nos permite poner a tu alcance soluciones novedosas y eficientes cuando lo necesites.
Innovación gracias a nuestra especialización
La innovación es un factor clave en NORTEK. Contamos con un equipo de ingenieros listos para afrontar nuevos desafíos y aportan un servicio de asesoramiento, de manera proactiva, tanto de desarrollos innovadores de tecnologías ya existentes como productos radicalmente nuevos. Estos proyectos pasan, además, por pruebas exhaustivas, primero en condiciones de laboratorio y, posteriormente, en campo.
¿Cómo puede ayudarte nuestra labor en investigación y desarrollo?
Son muchas las ventajas que obtendrás derivadas del trabajo en investigación y desarrollo, entre las que destacamos:
- Desarrollo de nuevas tecnologías de filtración, separación de fluidos y transferencia de calor
- Investigación en nuevos sistemas de enfriamiento
- Investigación en sistemas de distribución de fluidos (particularmente, de lubricación)
- Desarrollo de nuevos sistemas de optimización de procesos industriales relacionados con fluidos
- Innovación en métodos de fabricación interna para productos
- Impresión 3D
El hecho de contar con un taller polivalente propio y con equipos de alto nivel de profesionalidad, expertos de asistencia on-site, nos permite orientar nuestros desarrollos no solo a productos eficientes y rentables en sí mismos, sino también a la viabilidad y optimización de su fabricación, montaje y operación.
Montaje, puesta en marcha y mantenimiento de procesos industriales
Un producto diseñado de principio para las necesidades del cliente, que requiere de un montaje cuidadoso para una correcta implantación.
Además de nuestro propio personal de taller, tienes a tu disposición a todo un equipo de montadores de campo, que incluye especialistas en tubería, hidráulica y soldadura. De esta forma contarás con un servicio de montaje de calidad contrastada, centrado en lograr ejecuciones cuidadas en tiempos mínimos, con especial atención a las particularidades y requerimientos de cada proyecto.
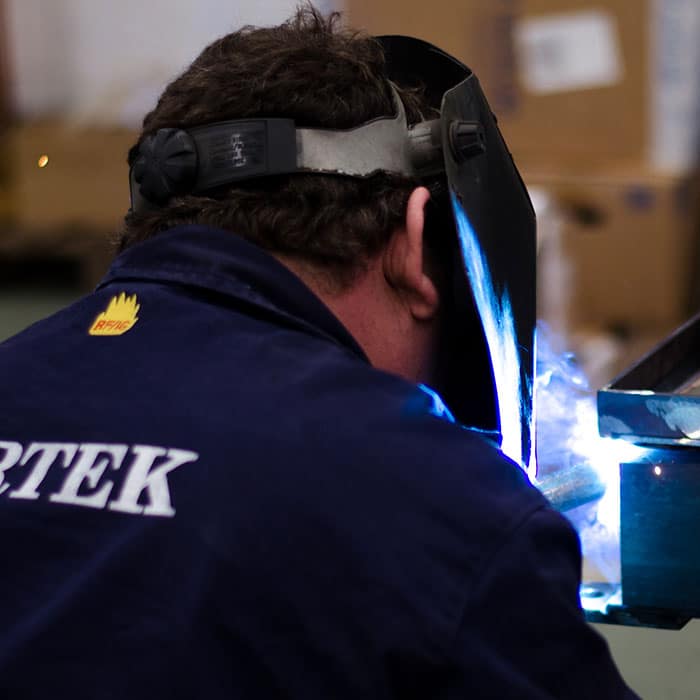
Algunas de nuestras competencias en este campo son:
- Instalación de equipos de lubrificación
- Fabricación en campo e instalación de tuberías de cualquier dimensión
- Ejecución de instalaciones de agua, aire, hidráulicas y de lubrificación con aceite, grasa o aire-aceite
- Puesta en marcha de equipos
- Supervisión especializada de montajes
- Asesoría con equipos (troubleshooting)
- Mantenimiento periódico de los equipos de lubrificación en la planta del cliente
- Mantenimiento específico de instalaciones durante paradas de la producción
- Reparación de bombas
- Reparación y repintado de depósitos
- Recuperación para su uso de equipos de engrase, separadores magnéticos, sistemas de deshidratación por vacío…
Llevamos nuestra tecnología de fluidos por todo el mundo
Los ingenieros y técnicos de campo de NORTEK cuentan también con una larga experiencia en la supervisión de montajes y en la ejecución de puestas en marcha on-site.
Nuestra vocación exportadora y el elevado nivel de complejidad de algunos de los proyectos que hemos afrontado nos distingue: estamos preparados para viajar a lo largo del mundo y para adaptarnos a las condiciones culturales y técnicas de cualquier destino.
Contamos, además, con personal especializado en mantenimiento de instalaciones de lubrificación on-site, que ofrecemos tanto en clave de presencia periódica como para momentos específicos de parada o replanteamiento del sistema. Ello se ve complementado con la disponibilidad de nuestro taller para efectuar reparaciones profundas de equipos cuyo aprovechamiento se desea prolongar.
Asesoramiento y atención post-venta
La entrega de tu producto terminado es sólo el primer paso.
Creemos firmemente en las relaciones a largo plazo basadas en la confianza, y lo mostramos a través de nuestra implicación antes, durante y después de tu pedido. Porque conocemos la tranquilidad que supone estar respaldado por un equipo de expertos capaces de asesorarte, y atender cualquier incidencia, en un corto periodo de tiempo.
Te acompañamos en el camino hacia un funcionamiento óptimo de nuestros sistemas gracias a la elaboración de documentación precisa, el seguimiento proactivo de incidencias, la asistencia técnica capacitada y una rápida respuesta en el suministro de repuestos.
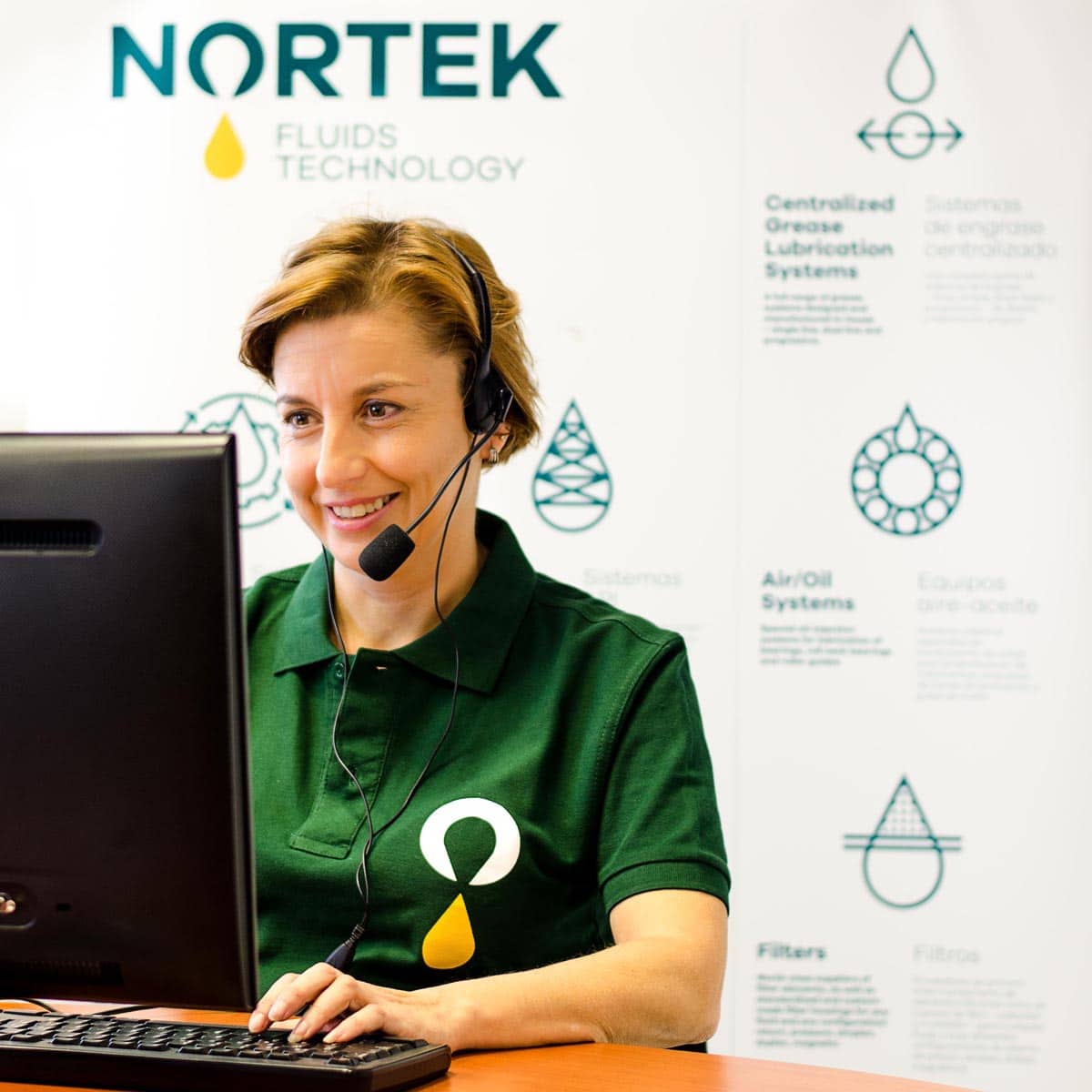
Ingenieros y fabricantes: lo tienes todo a tu favor
Nuestra doble condición de ingenieros y fabricantes nos faculta para ofrecerte asesoramiento directo sobre las modificaciones técnicas necesarias para adaptar la configuración de nuestros sistemas, en el caso de que se produzcan variaciones sobre las condiciones de operación iniciales.
Estos son algunos de los servicios que distinguen nuestra política de atención post-venta:
- Seguimiento de los equipos instalados
- Asesoramiento técnico post-venta
- Acompañamiento al cliente en el caso de cambios en los parámetros de operación
- Suministro de repuestos NORTEK originales y garantizados
Formación y consultoría: transferencia de conocimiento
Compartimos contigo nuestro conocimiento en tecnología de fluidos
Somos conscientes de la importancia de la formación del personal técnico para mejorar aún más sus competencias y, por eso, ofrecemos formaciones específicas en en nuestras instalaciones o bien en tu propia empresa.
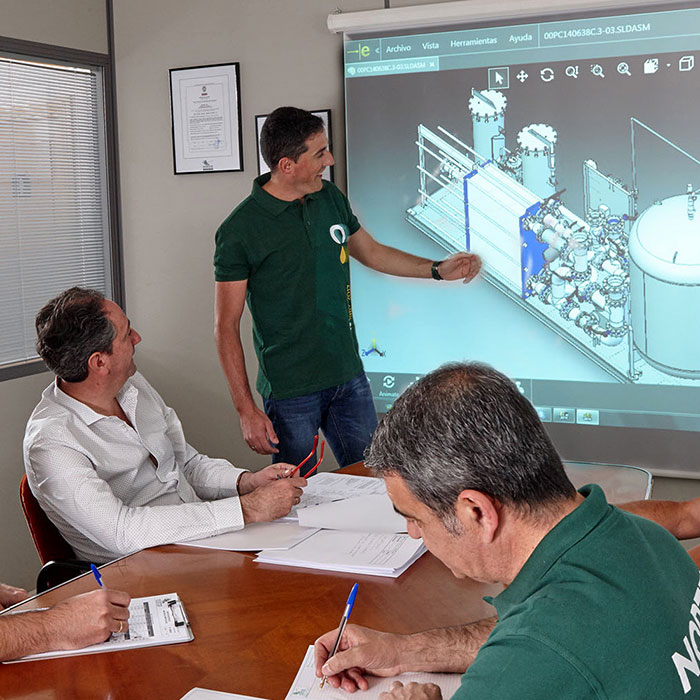
En concreto, te ofrecemos:
- Sesiones formativas sobre tribología
- Cursos específicos en el cliente sobre lubricación, sistemas de grasa, deshidratación de aceites por vacío, sistemas de filtración y sistemas de fluidos (incluyendo sistemas de enfriamiento, hidráulica y neumática).
- Sesiones formativas en nuestros talleres sobre puesta en marcha de equipos NORTEK
A lo largo de nuestra dilatada trayectoria hemos sido requeridos en multitud de ocasiones para formar a personal técnico tanto en las bases teóricas de nuestra ingeniería de fluidos como en la vertiente práctica del funcionamiento de nuestros sistemas. Nuestros ingenieros y técnicos de taller están a tu disposición del cliente para facilitar esta transferencia de saber y favorecer un conocimiento más profundo de los equipos que suministramos.
Empresas que confían en Nortek
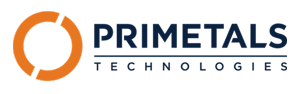
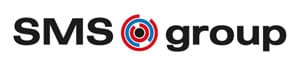
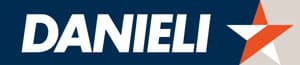
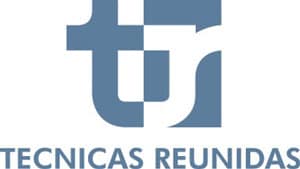
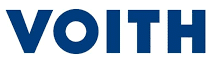

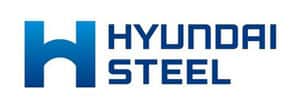

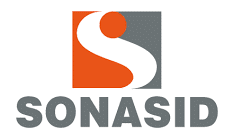
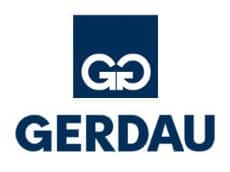
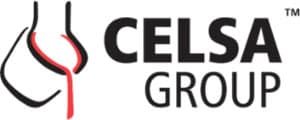
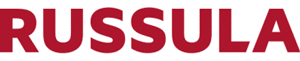
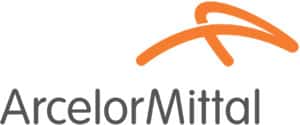
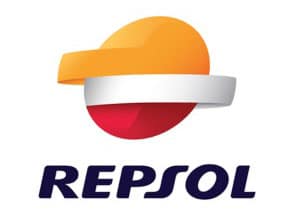
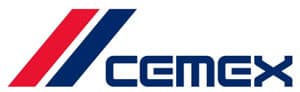
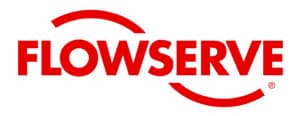
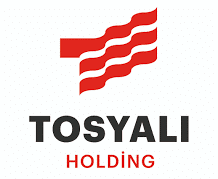
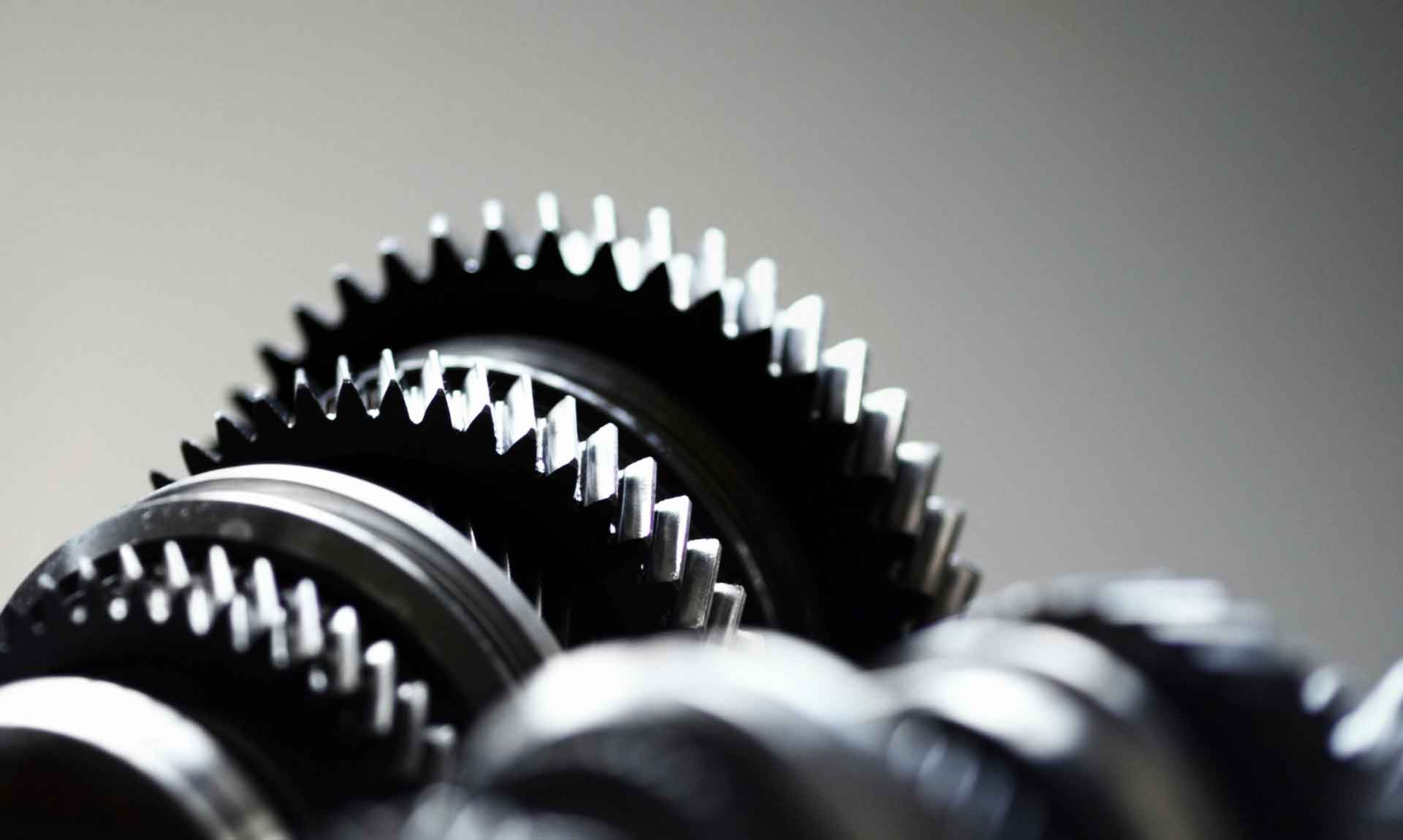
Trabajamos bajo las directrices de la norma ISO 9001:2015
Calidad y eficiencia
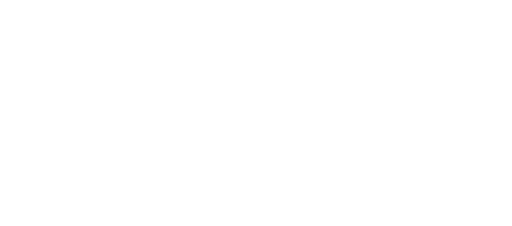
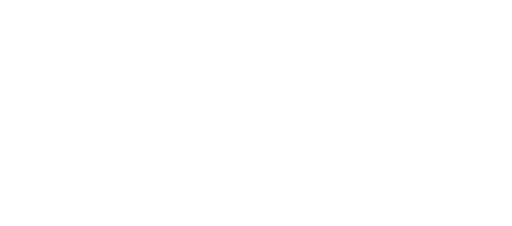
Todos los miembros de NORTEK deben conocer la política de calidad, comprenderla y asumirla como propia; y todos ellos están también llamados a contribuir a la tarea permanente de evaluarla, adaptarla y mejorarla.