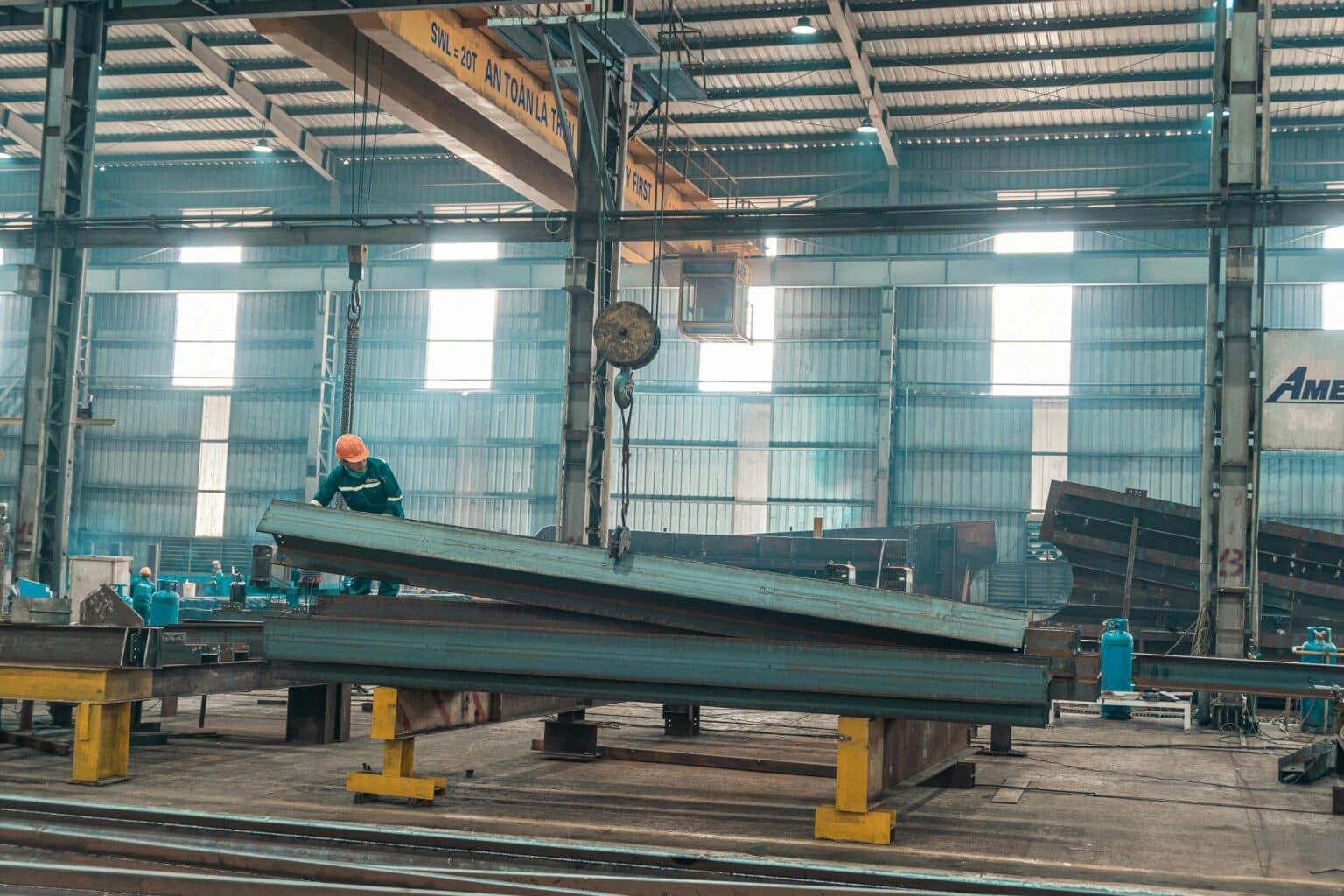
¿Qué es una parada técnica y por qué es necesaria en la industria?
Las paradas técnicas (también conocidas como paradas de mantenimiento) dan lugar en empresas de índole industrial, habitualmente durante la temporada de verano o invierno. Esto es así debido a que, durante estas fechas, suele haber periodos vacacionales, lo que lleva a las empresas a parar o ralentizar sustancialmente la producción.
Quédate a leer este artículo para saber en qué consisten estas paradas, por qué son importantes y como efectuarlas con la mayor eficiencia posible.
¿Qué es una parada técnica o de mantenimiento?
Una parada técnica es un proceso realizado por fábricas y otras empresas industriales con el fin de realizar trabajos de carácter preventivo o reparaciones necesarias. También se pueden dedicar estas paradas a realizar mejoras en la capacidad productiva o en las instalaciones en general.
Para poder realizar este proceso, se ha de parar total o parcialmente el proceso productivo de la fábrica, por lo que se necesita tanto una buena planificación como un nivel de recursos suficiente para que el proceso no se alargue más de lo necesario.
¿Por qué son importantes las paradas técnicas para el mantenimiento y la seguridad?
Las paradas, si se realizan de manera organizada, pueden suponer una garantía, tanto para la continuidad eficiente a largo plazo del proceso productivo como para la seguridad de los trabajadores y del entorno laboral. A continuación, os explicamos todas las dimensiones de esta influencia.
Mejora de la eficiencia y productividad
Una parada técnica bien planificada permite la revisión, mantenimiento y actualización de equipos y sistemas industriales. Este proceso es fundamental para identificar y corregir problemas antes de que se conviertan en fallos mayores, lo que a su vez reduce el tiempo de inactividad no planificado.
Este proceso se lleva a cabo mediante el mantenimiento proactivo de los equipos y la actualización de estos, logrando así un aumento directo o indirecto de la eficiencia y la productividad.
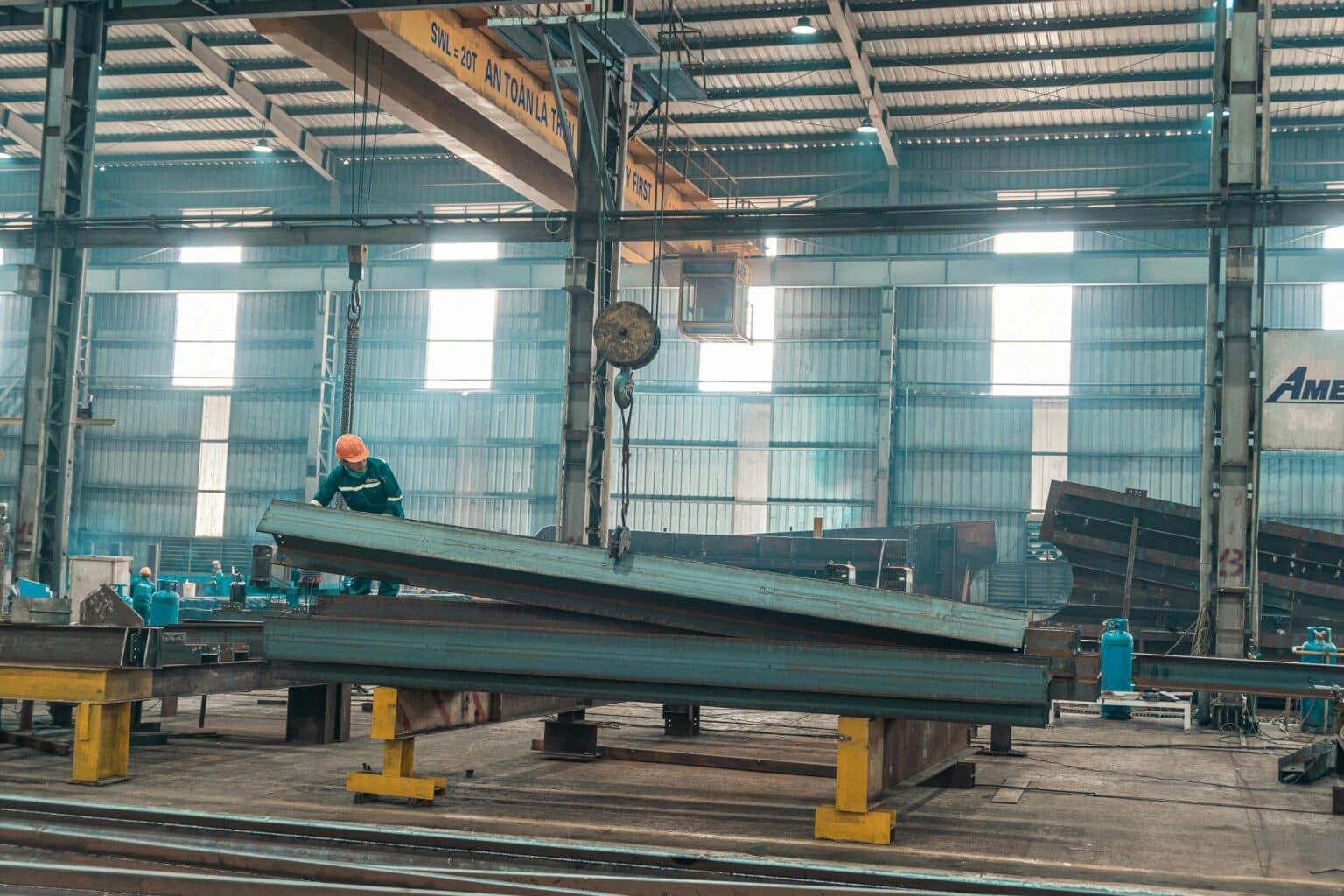
Aumento de la seguridad
La seguridad tiene que ser la primera prioridad de cualquier entorno de carácter industrial. Las paradas técnicas desempeñan un papel crucial en la identificación y mitigación de riesgos potenciales que podrían poner en peligro a los trabajadores y la infraestructura.
Se pueden aprovechar las paradas técnicas en este sentido tanto para realizar inspecciones de seguridad que detecten y corrijan los posibles errores de las instalaciones como para capacitar al personal en nuevas normas y procesos.
Reducción de Costos Operativos
Aunque las paradas técnicas requieren una inversión inicial en tiempo y recursos, a largo plazo, son una estrategia efectiva para reducir los costos operativos generales.
Esto es así debido a que pueden evitar futuras reparaciones costosas y mejorar el uso de recursos de la empresa, disminuyendo así los gastos que estos suponen.
Cumplimiento de Normativas
Las industrias están sujetas a diversas normativas y estándares que regulan la seguridad, el medio ambiente y la eficiencia operativa. Las paradas técnicas son momentos clave para asegurar que estas regulaciones se cumplan o para actualizar los procesos que regulan.
Durante las paradas se pueden realizar auditorías, obtenciones de certificaciones y actualizaciones de protocolos.
¿Cómo optimizar las paradas técnicas?
El punto clave que optimiza al máximo las paradas de mantenimiento reside en la planificación previa. Esta tiene como base el mantenimiento predictivo, que se encarga de predecir las posibles averías antes de que sucedan. Por tanto, es fundamental tener este tipo de mantenimiento completamente monitorizado y aplicado.
Para poder optimizar entonces las paradas técnicas, se debe trabajar en una fase de organización previa que defina a la perfección todos los aspectos relacionados con la parada, como su duración, los recursos necesarios para ejecutarla y los contratiempos que puedan surgir.
Aun así, el resto de los procesos de mantenimiento también tienen influencia en las paradas técnicas. Teniendo un plan de mantenimiento que apueste fuertemente por prevenir y detectar con antelación los errores y que corrija estos cuando no quede otro remedio, se conseguirá reducir al máximo las paradas de mantenimiento y que resulten lo más eficientes posible.