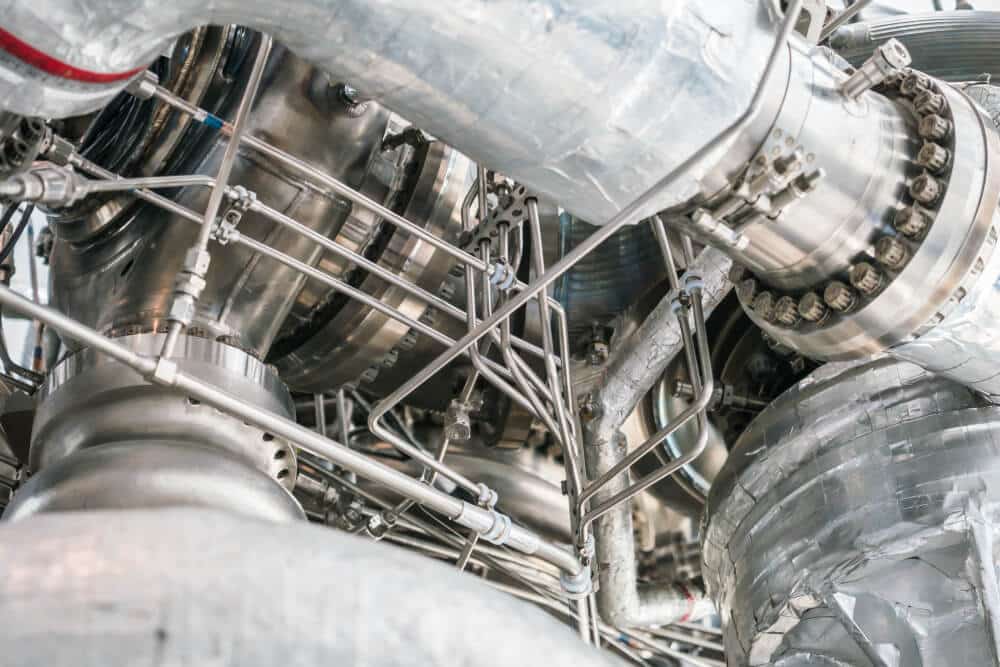
Guía completa de sistemas de lubricación industrial automatizada
En el mundo industrial actual, la eficiencia y la fiabilidad de la maquinaria son fundamentales para el éxito. Los sistemas de lubricación industrial automatizados representan una solución avanzada para optimizar el mantenimiento y asegurar el funcionamiento continuo de los equipos. Esta guía completa explorará en detalle qué son estos sistemas, cómo funcionan y por qué la inversión en la automatización de la lubricación es crucial para las empresas modernas.
¿Qué es un sistema de lubricación automática?
Un sistema de lubricación automática, también conocido como sistema de engrase automático, es un dispositivo diseñado para suministrar lubricante a múltiples puntos de lubricación de una máquina o equipo de manera controlada y sin intervención manual. A diferencia de la lubricación manual, que depende del operador y puede resultar en lubricación insuficiente o lubricación excesiva, los sistemas automáticos garantizan una lubricación constante y precisa. Estos sistemas centralizan la lubricación desde un único punto, asegurando que cada punto de lubricación reciba la cantidad correcta de lubricante en los ciclos de lubricación según lo programado. El objetivo principal es prolongar la vida útil de los componentes, minimizar el tiempo de inactividad y reducir los requisitos de mantenimiento. La lubricación automatizada es especialmente valiosa en maquinaria compleja con múltiples puntos de lubricación o en entornos peligrosos donde la lubricación manual sería difícil o riesgosa.
Componentes clave
Los sistemas de lubricación automatizados constan de varios componentes interconectados que trabajan en conjunto para garantizar una lubricación eficaz y precisa. Estos componentes clave incluyen bombas, válvulas, sensores y controladores, cada uno desempeñando un papel crucial en el proceso de lubricación.
Bombas
Las bombas son el corazón del sistema de lubricación, encargadas de suministrar el lubricante desde el depósito hasta los puntos de lubricación. Existen diferentes tipos de bombas, como las bombas de engranajes, bombas de pistón y bombas peristálticas, cada una adecuada para diferentes tipos de lubricantes y aplicaciones. La elección de la bomba depende de la viscosidad del lubricante, la presión requerida y el caudal necesario para lubricar adecuadamente cada punto de lubricación. La bomba debe ser capaz de mantener una lubricación constante y fiable, incluso en condiciones de alta demanda. La capacidad de la bomba se dimensiona según la cantidad de múltiples puntos de lubricación que deben ser atendidos, garantizando que el sistema de lubricación automática pueda mantener los niveles de lubricación óptimos en todo momento.
Válvulas
Las válvulas en un sistema de lubricación automática controlan el flujo de lubricante hacia los diferentes puntos de lubricación. Estas válvulas pueden ser de diferentes tipos, incluyendo válvulas de control de flujo, válvulas de alivio de presión y válvulas direccionales. Su función principal es regular la cantidad de lubricante que llega a cada punto, asegurando una lubricación precisa y evitando la lubricación excesiva o insuficiente. En los sistemas progresivos de línea única y sistemas de doble línea, las válvulas juegan un papel crucial en la distribución secuencial del lubricante. La selección adecuada de las válvulas es esencial para el rendimiento y la eficiencia del sistema de lubricación.
Sensores
Los sensores son componentes vitales para supervisar el estado del sistema de lubricación y garantizar su correcto funcionamiento. Estos sensores pueden medir diferentes parámetros, como la presión del lubricante, el nivel del depósito, la temperatura y el caudal. Al supervisar estos niveles de lubricación, los sensores pueden detectar anomalías y alertar al sistema de control o al operador sobre posibles problemas, como fugas, bloqueos o niveles bajos de lubricante. La información proporcionada por los sensores permite tomar medidas correctivas de manera oportuna, evitando daños mayores a la maquinaria y reduciendo el tiempo de inactividad. La integración de sensores en los sistemas automatizados mejora significativamente la fiabilidad y la eficiencia de la lubricación.
Controladores
Los controladores son el cerebro del sistema de lubricación automática, encargados de gestionar y coordinar todos los componentes. Estos controladores pueden ser simples temporizadores o sistemas más sofisticados basados en microprocesadores, dependiendo de la complejidad de la aplicación. El controlador permite programar los ciclos de lubricación, ajustar la cantidad de lubricante suministrado y recibir información de los sensores para realizar ajustes en tiempo real. Además, el controlador puede registrar datos sobre el rendimiento del sistema, facilitando el mantenimiento preventivo y la detección de problemas potenciales. En los sistemas de lubricación multipunto, el controlador asegura que cada punto de lubricación reciba la cantidad adecuada de lubricante en el momento preciso, optimizando la lubricación y prolongando la vida útil de la maquinaria.
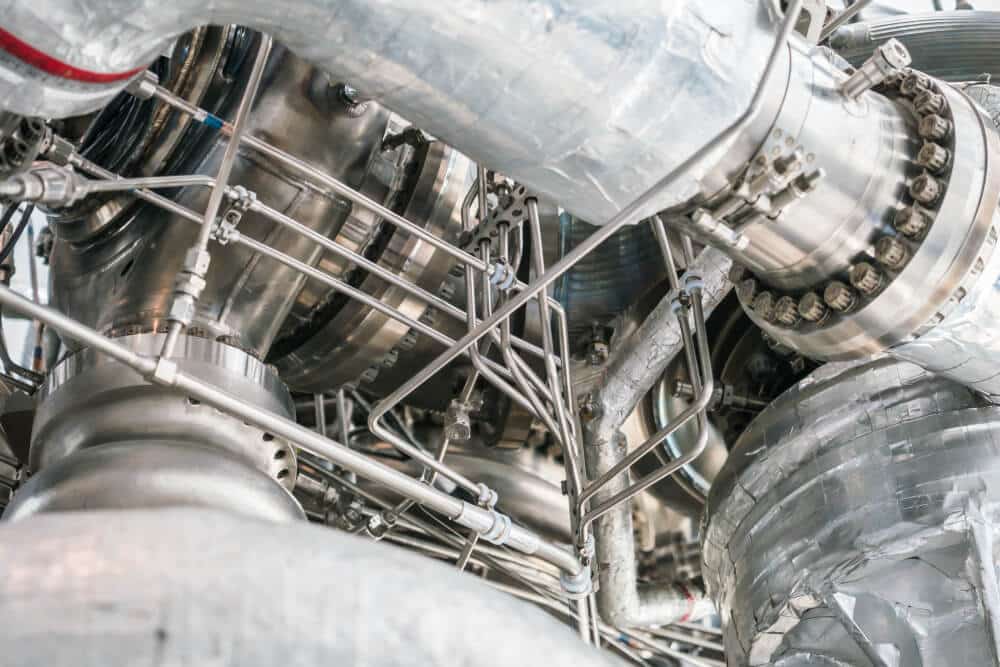
Beneficios
El hecho de utilizar tecnología de lubricación automática en tus instalaciones te permite disfrutar de las siguientes ventajas:
Ahorro en aceite
Uno de los beneficios más significativos de implementar un sistema de lubricación automática es el ahorro en aceite. Los sistemas automatizados están diseñados para suministrar la cantidad precisa de lubricante necesaria en cada punto de lubricación, evitando la lubricación excesiva que a menudo ocurre con la lubricación manual. Este control preciso no solo reduce el consumo total de lubricante, sino que también minimiza el riesgo de contaminación y derrames, lo que conlleva ahorros adicionales en costos de limpieza y disposición de residuos. Al centralizar la lubricación desde un único punto, se facilita la gestión y el control del lubricante, optimizando su uso y reduciendo los costos operativos. Además, la lubricación constante y adecuada proporcionada por los sistemas automáticos ayuda a prolongar la vida útil de los componentes, reduciendo la necesidad de reemplazos frecuentes y los costos asociados.
Reducción de tiempo de inactividad
La reducción del tiempo de inactividad es otro beneficio crucial de los sistemas automatizados. Al garantizar una lubricación constante y adecuada, estos sistemas minimizan el desgaste y la fricción en los componentes de la maquinaria, previniendo fallas y averías inesperadas. La lubricación precisa que cada punto de lubricación recibe reduce la probabilidad de paradas no planificadas, lo que a su vez aumenta la disponibilidad y la productividad de los equipos. Los sistemas de lubricación automática también facilitan el mantenimiento preventivo, ya que permiten supervisar los niveles de lubricación y detectar problemas potenciales antes de que causen interrupciones mayores. Al reducir el tiempo de inactividad, las empresas pueden optimizar su producción, cumplir con los plazos de entrega y mejorar su rentabilidad general. Además, se disminuyen los requisitos de mantenimiento y, al prolongar la vida útil de las máquinas, se minimiza la necesidad de reparaciones costosas.
Casos de uso
Los sistemas de lubricación automática pueden ir dirigidos a cualquier tipo de aplicación o industria, siempre que adaptes la instalación a las necesidades de tus máquinas. Algunos de los sectores que se benefician de sistemas de lubricación automática son los siguientes:
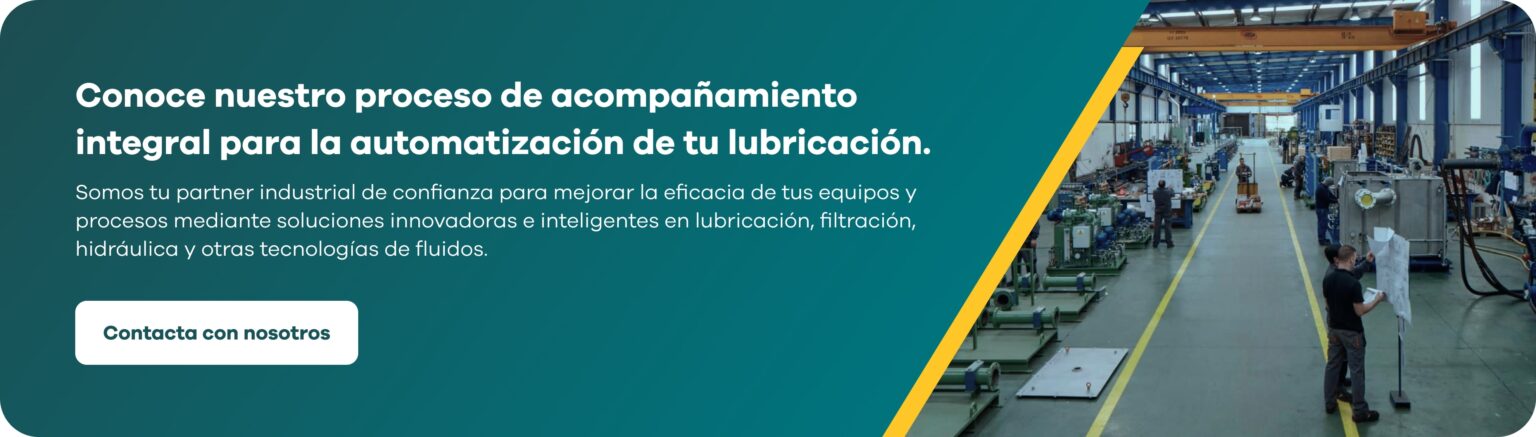
Industria siderúrgica
En la industria siderúrgica, la maquinaria pesada como laminadores, grúas y transportadores opera en condiciones extremas de temperatura y carga. Un sistema de lubricación automático es esencial para garantizar que cada punto de lubricación reciba la cantidad adecuada de lubricante. Los sistemas automatizados ayudan a prolongar la vida útil de los rodamientos y otros componentes críticos, minimizando el tiempo de inactividad y reduciendo los requisitos de mantenimiento. La lubricación constante proporcionada por un sistema de lubricación mejora la eficiencia operativa y reduce los costos de reparación. Al centralizar la lubricación desde un único punto, se facilita la gestión del lubricante y se reduce el riesgo de lubricación excesiva o lubricación insuficiente. Los tipos de sistemas de lubricación implementados en este sector suelen ser robustos y diseñados para manejar altas cargas y temperaturas.
Industria minera
La industria minera se enfrenta a desafíos únicos debido a la exposición constante a polvo, suciedad y condiciones ambientales adversas. En este contexto, un sistema de lubricación automático es crucial para proteger la maquinaria pesada, como excavadoras, camiones de transporte y trituradoras. Estos sistemas automáticos aseguran que cada punto de lubricación reciba la cantidad necesaria de lubricante para combatir el desgaste y la corrosión. Los sistemas de lubricación multipunto son ideales para estas aplicaciones de los sistemas, donde hay múltiples puntos de lubricación que requieren atención constante. Al supervisar los niveles de lubricación y suministrar el lubricante de manera precisa, se minimiza el tiempo de inactividad y se optimiza la productividad. El uso de la lubricación automatizada también reduce la necesidad de lubricación manual, lo que mejora la seguridad de los operarios y disminuye los requisitos de mantenimiento. La lubricación precisa también ayuda a reducir la fricción y el consumo de energía.
Industria petroquímica
En la industria petroquímica, donde se manejan sustancias peligrosas y las condiciones operativas son exigentes, la fiabilidad de la maquinaria es primordial. Un sistema de lubricación automático garantiza que los equipos críticos, como bombas, compresores y válvulas, operen de manera eficiente y segura. Estos sistemas automáticos pueden ser programados para suministrar el lubricante en ciclos de lubricación según las necesidades específicas de cada punto de lubricación. La lubricación constante proporcionada por estos tipos de sistemas de lubricación ayuda a prolongar la vida útil de los componentes, minimizando el riesgo de fallas y reduciendo el tiempo de inactividad. Al supervisar continuamente los niveles de lubricación, se pueden detectar problemas potenciales antes de que causen interrupciones costosas. Además, la lubricación automatizada reduce la exposición de los trabajadores a entornos peligrosos y optimiza el uso del lubricante, evitando la lubricación excesiva y reduciendo los costos operativos. La implementación de un sistema de lubricación bien diseñado es esencial para mantener la seguridad y la eficiencia en la industria petroquímica.
Claves para elegir el sistema adecuado
Seleccionar el tipo de sistema de lubricación automatizada adecuado para una aplicación industrial específica es crucial para maximizar sus beneficios. Es fundamental evaluar cuidadosamente las necesidades de lubricación de la maquinaria, considerando factores como el número de puntos de lubricación, el tipo de lubricante requerido, las condiciones operativas y los requisitos de mantenimiento. Los sistemas progresivos de línea única son ideales para aplicaciones con un número moderado de puntos de lubricación, mientras que los sistemas de doble línea son más adecuados para aplicaciones con un gran número de puntos de lubricación y distancias más largas. Los sistemas paralelos de línea única ofrecen flexibilidad y pueden ser adaptados a una variedad de aplicaciones de los sistemas. Además, es importante considerar la calidad de los componentes del sistema de lubricación, como las bombas, las válvulas y los sensores, para garantizar su fiabilidad y durabilidad. Al elegir un sistema de lubricación, también se debe tener en cuenta la facilidad de instalación, operación y mantenimiento, así como el soporte técnico ofrecido por el proveedor.
Contáctanos si quieres saber más respecto a lo que un sistema de lubricación automática puede aportar a tu empresa o si tienes alguna duda.